Common Issues Solved by Expert Packaging Machine Repair Technicians
Expand the Life of Your Packaging Tools With Expert Repair Service
Involving specialist repair solutions not only addresses immediate mechanical and electrical concerns yet also cultivates a society of normal upkeep that can dramatically boost devices efficiency. Comprehending the full extent of advantages and the best strategy to picking a repair solution can be critical, leading to a much more calculated investment in your equipment.
Value of Routine Maintenance
In the realm of packaging equipment, the significance of regular upkeep can not be overemphasized. Routine upkeep makes sure that equipment operates effectively, reducing the probability of unanticipated malfunctions that can disrupt production timetables. Regular maintenance entails systematic assessments, cleansing, lubrication, and adjustments that are crucial for optimal performance.
Additionally, upkeep functions as a positive strategy to identifying prospective concerns before they escalate right into expensive repairs. By attending to small damage quickly, services can expand the life-span of their equipment, securing their funding financial investments. This preventative approach not only minimizes downtime but likewise improves general efficiency.
Furthermore, routine maintenance plays an essential duty in ensuring compliance with safety standards and policies. Properly maintained equipment is much less likely to present security dangers to operators, thus fostering a safer working environment. It also aids in keeping item high quality, as appropriately working equipment is vital in adhering to specifications and decreasing issues throughout the packaging process.
Advantages of Specialist Repair Work

Moreover, professional repair services often utilize top quality parts and materials that go beyond or fulfill supplier specs. This dedication to high quality guarantees that the repaired tools runs at ideal performance degrees, lengthening its life expectancy and minimizing the possibility of future malfunctions.
Furthermore, expert repair can result in cost financial savings with time (packaging machine repair). By resolving problems immediately and effectively, organizations can stay clear of the high expenses connected with full tools replacements. Regular specialist maintenance can maximize the performance of product packaging devices, leading to increased performance and, consequently, greater success.
Lastly, depending on professionals for repairs cultivates compliance with sector standards and safety and security policies, mitigating threats connected with inappropriate handling of equipment. Fundamentally, purchasing professional repair service services not only endures equipment performance yet also adds to a more effective, secure, and profitable operational environment.
Typical Packaging Devices Issues
Recognizing common product packaging equipment issues is essential for maintaining functional effectiveness. Packaging equipment commonly faces a variety of troubles that can interfere with manufacturing and compromise product integrity. One common concern is mechanical failure, which can stem from worn-out elements, misalignment, or lack of lubrication. Such failings might cause unanticipated downtime and pricey repairs (packaging machine repair).
One more typical problem is electrical malfunctions. These can arise from damaged circuitry, blown integrates, or obsolete control systems. Electric issues can trigger devices to run erratically or fall short to begin entirely, impacting the whole product packaging line.
Additionally, product jams regularly take place as a result of incorrect configuration, debris buildup, or worn parts. Jams not just stop production but might likewise damage the products being refined, causing additional losses.
Additionally, irregular securing or labeling can occur from look at this website equipment wear or wrong calibration, weakening product top quality and conformity with industry criteria. Last but not least, insufficient maintenance techniques usually add to a decline in devices performance, making normal assessments and servicing important. By recognizing and resolving these common problems, companies can improve their product packaging operations and lengthen the lifespan of their equipment.
Picking the Right Repair Work Solution
Selecting the ideal repair service for product packaging equipment is vital to minimizing downtime and making certain functional efficiency. When examining prospective company, consider their knowledge and expertise in the kind of tools you make use of. A business with a proven record in your details machinery will likely use more dependable and effective repair work.
Furthermore, analyze the qualifications and accreditations of the professionals. Experienced experts who are skilled in market requirements can recognize concerns quicker and carry out remedies much more successfully. Looking into customer reviews and testimonies can additionally provide understanding right into the company's online reputation and reliability.
Another important factor is the availability of emergency situation assistance. Devices failures can occur all of a sudden, and having access to a receptive repair solution can significantly reduce the influence of downtime. Moreover, inquire concerning the service warranty used on repair services, as this can reflect the self-confidence the company has in their work.
Lastly, take into consideration the communication and support framework of the repair solution. A business that prioritizes customer support will not just keep you educated throughout the repair service process yet will additionally be more probable to use ongoing upkeep recommendations to expand the life of your devices.
Price Cost Savings Via Expert Fixings
Just how can investing in expert fixings result in substantial cost savings for your product packaging tools? Engaging proficient service technicians for fixings makes sure that issues are accurately detected and efficiently dealt with, protecting against additional damages and costly downtime. Specialist repair work services use specialized expertise and devices, which can lead to much more effective upkeep than internal initiatives, subsequently lowering labor prices.
Moreover, timely repairs can extend the lifespan of your equipment, delaying the need for expensive replacements. By maintaining optimal functioning, you also enhance manufacturing performance, which converts to decrease functional expenses. When devices run smoothly, there is less waste, and productivity degrees continue to be high, permitting far better earnings margins.
In addition, specialist repair services usually feature service warranties or warranties, offering assurance and economic defense versus future failures. This assurance can minimize unforeseen costs and help with better budgeting for maintenance.
Finally, buying expert repair work services cultivates an aggressive strategy to tools administration, promoting a society of routine maintenance checks. This technique better improves overall tools dependability, ultimately bring about sustained price savings in the long run. Focusing on professional fixings is therefore a smart financial choice for companies reliant on product packaging devices.
Verdict
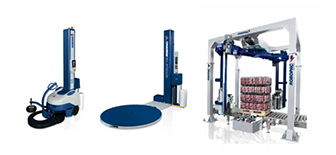
Engaging specialist repair work solutions not only addresses prompt mechanical and electrical concerns but additionally fosters a society of regular maintenance that can dramatically improve tools performance.Specialist repair service of packaging devices offers numerous benefits that can dramatically improve functional effectiveness.Just how can investing in specialist fixings lead to considerable cost savings for your packaging tools? Prioritizing expert fixings is therefore a smart financial decision for businesses reliant on product packaging tools.
In final thought, the longevity and effectiveness of product packaging tools can be significantly improved with normal upkeep and specialist repair solutions.